The Inventors of Micro-Blasting Technology
We believe your product is the most important in the world. That’s why we pioneered a complete micro-abrasive blasting system to help you make it even better.
What is Micro-Abrasive Blasting?
Micro-abrasive blasting is used to perform precision material removal. Our machines mix pressurized air with abrasive particles and blast them through a hose that is topped with a focused, hand-held nozzle. This process results in a highly accurate abrasive stream that can be used for cleaning, cutting, drilling, deburring, and finishing almost any surface.
The Basics
Airbrasive’s micro-abrasive blasting system uses a gas-propelled stream of uniformly-sized abrasive particles, finely controlled by a vibrator, to remove material from a work piece. The low inertia of the particles offers a way to accurately remove unwanted material from a surface without causing damage.
What makes Airbrasive’s system so versatile, however, is the various controls we’ve incorporated in our Micro-Blasting Units to offer our customers pinpoint precision. Air pressure, powder flow, nozzle size, and powder type can each be customized to provide the optimal solution for any project.
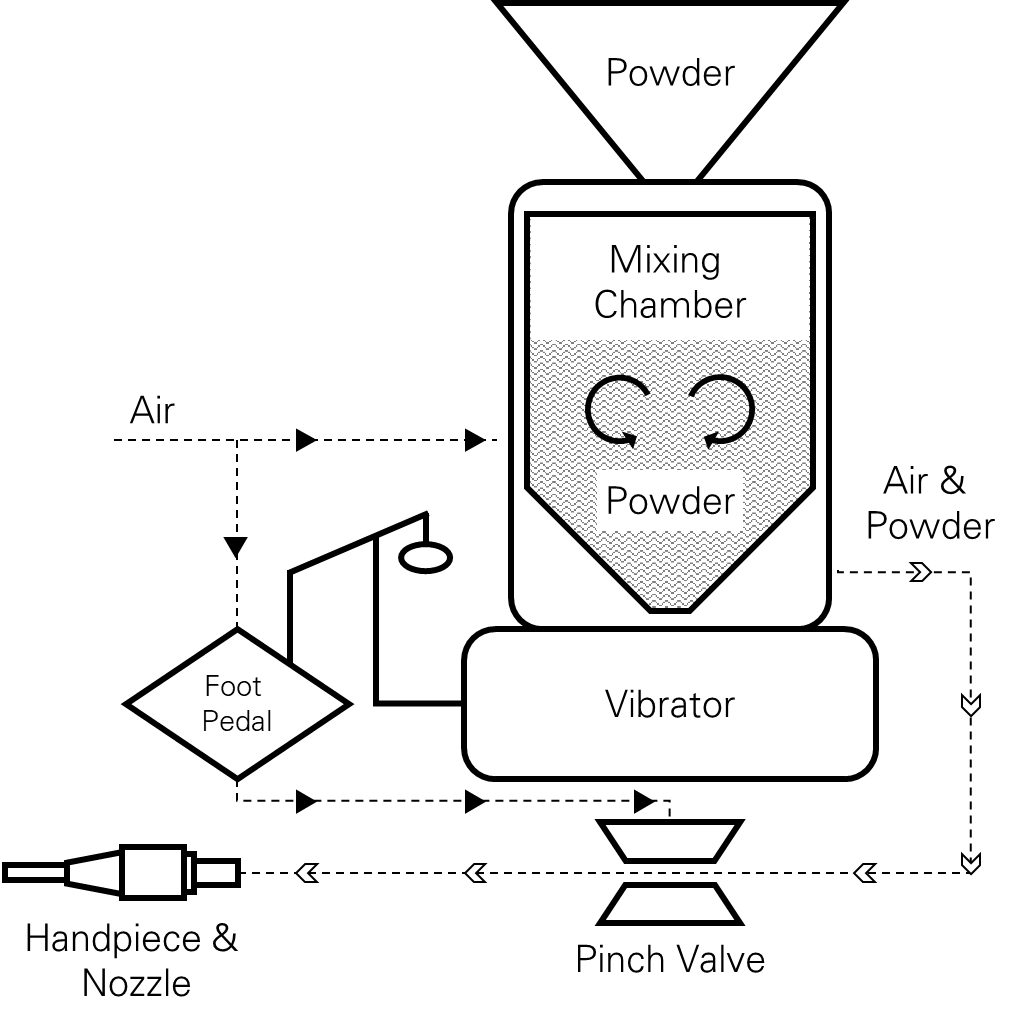
Powder Type
The most important variable in the micro-abrasive blasting process is the type of powder used. Airbrasive’s powders are blended from a variety of materials including aluminum oxide, glass beads, crushed glass, sodium bicarbonate, and silicon carbide. All of our powders are triple sifted to guarantee particle width uniformity down to the micron.
Powders range in their hardness. Harder media, like aluminum oxide and silicon carbide, are best used for more intense jobs like abrading, cutting, deburring, and drilling. Softer media, like glass bead and sodium bicarbonate, are best used for more delicate jobs like cleaning, peening, and coating removal.
Click here to download our powder selection guide. Our team will work with you to determine the best powder to suit your project’s needs.
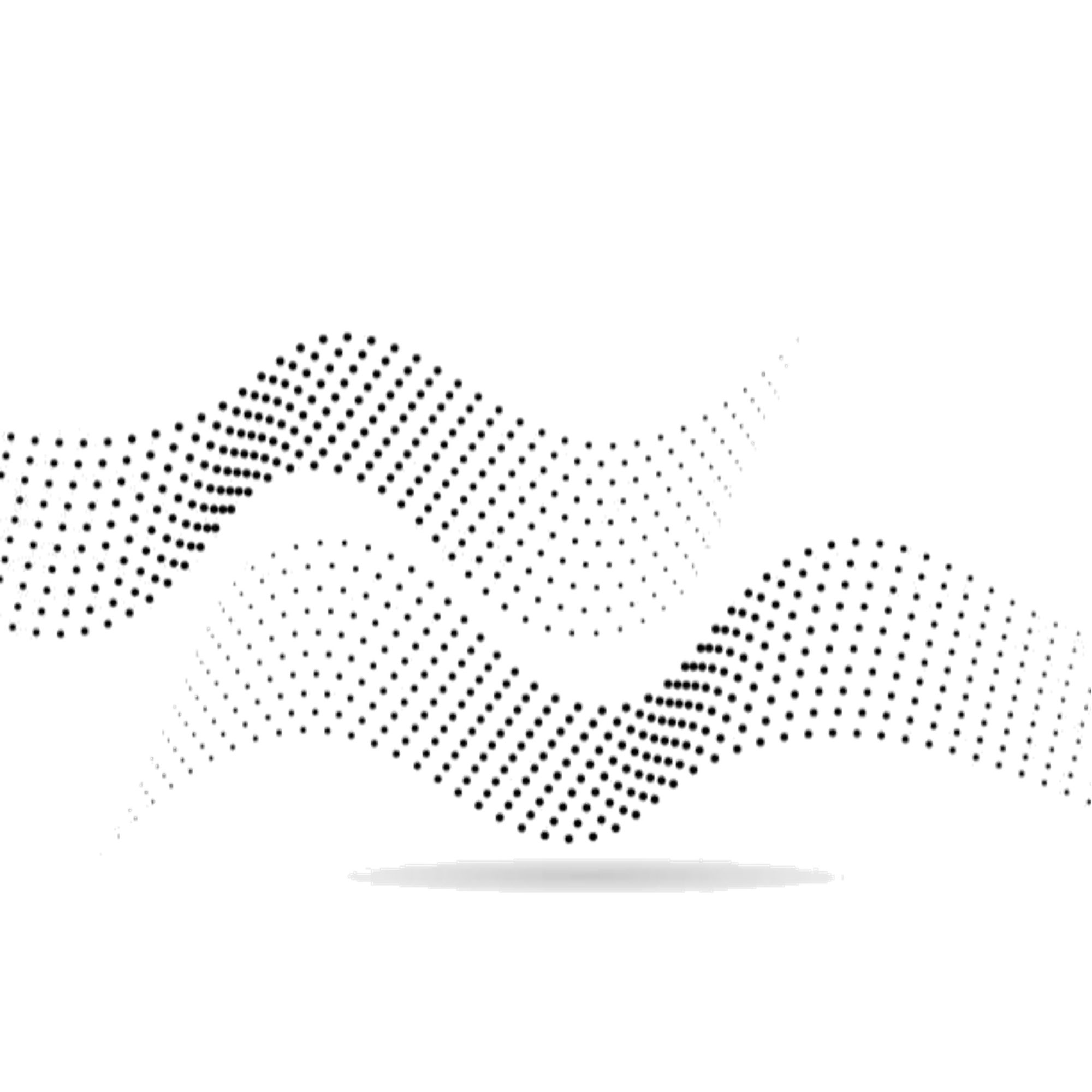
Air Pressure
Air pressure will directly affect the strength of the abrasive mixture and the machine’s ability to cut into various materials. The higher the air pressure, the stronger the stream, and therefore the more agitated the powder mixture will become. Likewise, lower air pressure can allow for gentler, more controlled abrasion. The amount of air pressure needed will depend on the type of project, material of the work piece, and the desired effect you wish to achieve.
The powder flow rate, which is the amount of powder that leaves the nozzle in one minute, will be directly impacted by the chosen air pressure. A higher powder flow rate will result in more precise cuts to your work surface.
Please note that for safety reasons the Airbrasive Micro-Abrasive Blasting Unit should never be pressurized beyond 120psi.
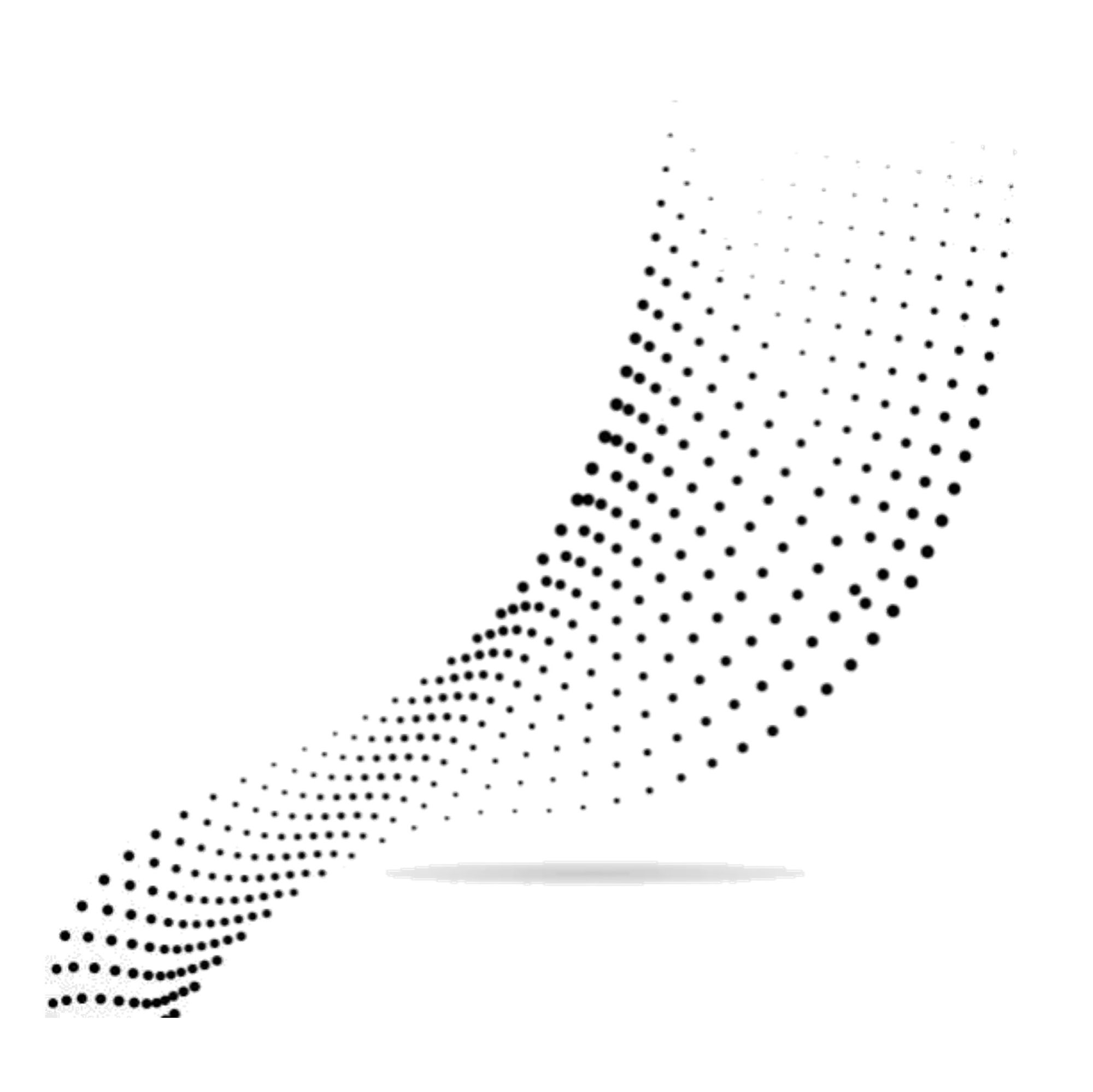
Nozzle Size
Nozzle orifices are usually either round or rectangular. The nozzle widths, ranging from .005” up to .032”, determine the surface area impacted by the powder – the larger the nozzle, the greater the surface area impacted.
The shape of the nozzle is important for getting into unusually shaped spaces. A rectangular nozzle can lightly cover a large width or, when turned, heavily impact a narrow space.
We offer a wide variety of nozzle types, orifice sizes, and orifice shapes to meet the needs of any project.
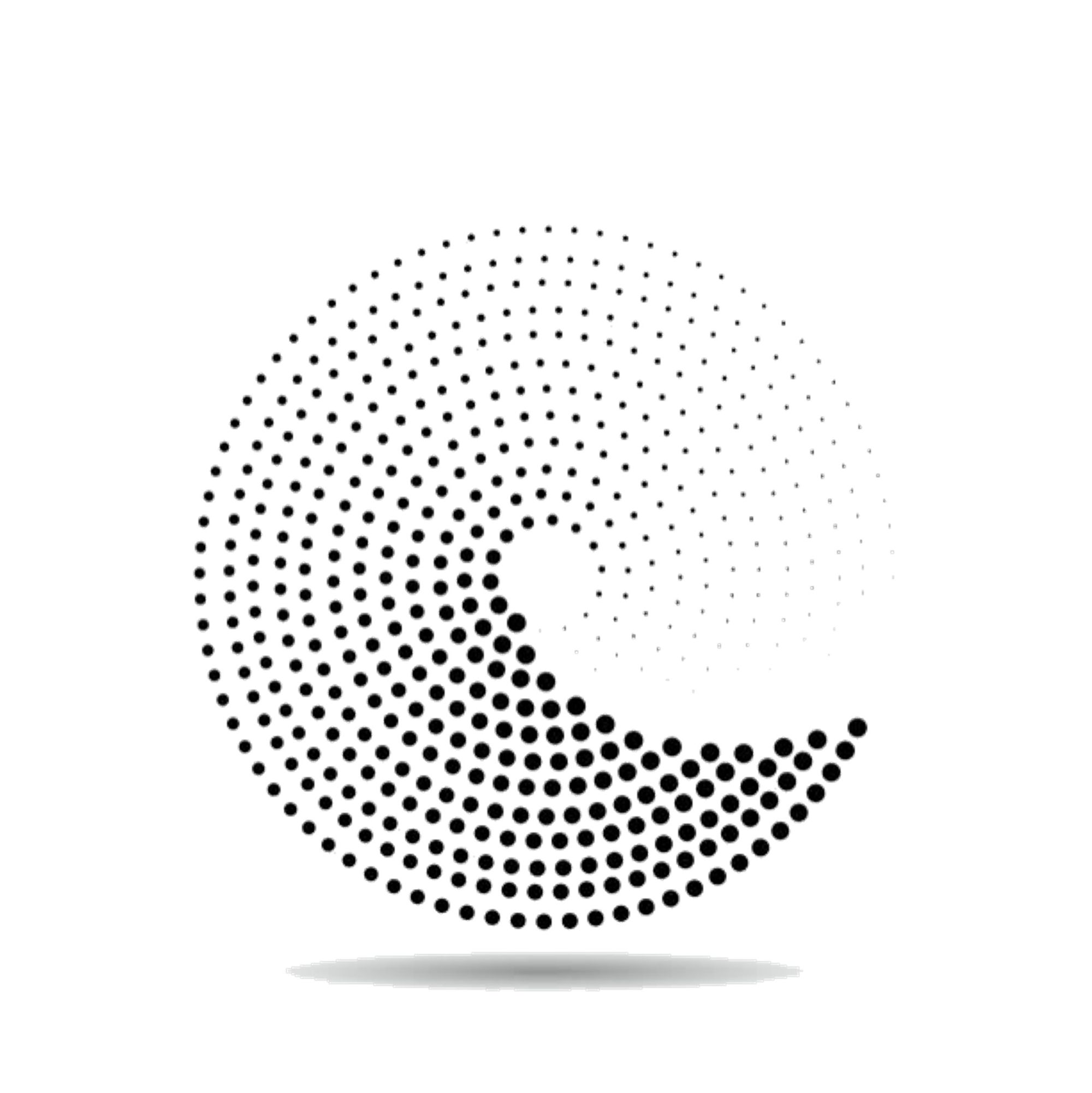
Contact Angle
The angle at which you blast the material surface will also affect the end result. By holding your nozzle at a 90° angle, abrasive stream and powder will more aggressively blast material off of the work surface. At an angle less than 90°, the air and powder mixture will instead steadily chip away at the material, allowing for more control of the process.
Tests have shown that maximum material removal for ductile materials occurs between a 15° and 45° angle of incidence. For a brittle material, maximum removal occurs at an angle of 90°.
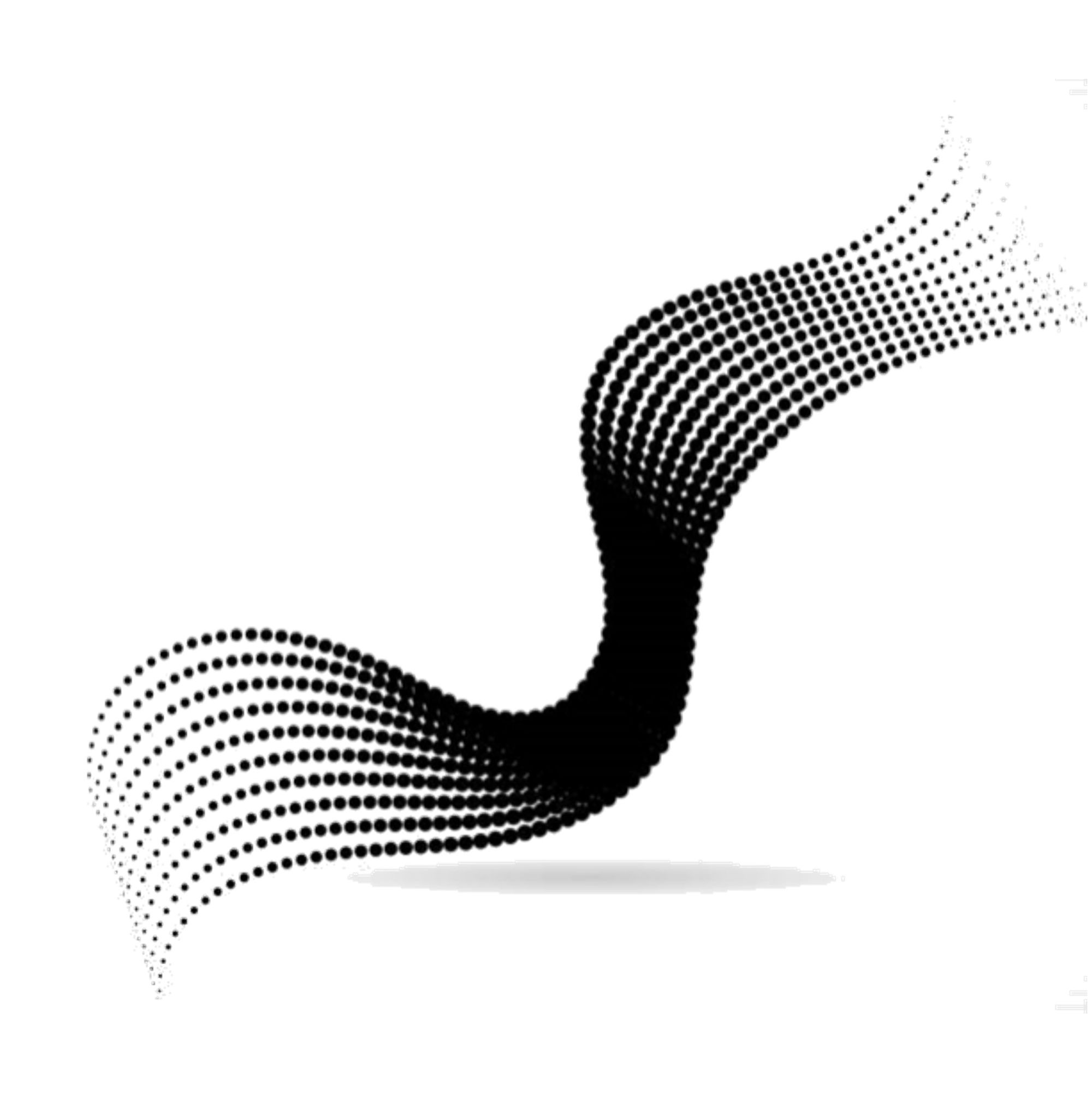
Our Micro-Abrasive Blasting Units
-
Model HME
View ProductWith its 20 lb. powder capacity, our Model HME unit gives producers the ability to micro-blast around the clock.
-
Model H
View ProductOur Model H unit enables high-volume micro-blasting in any environment, from laboratories to production lines.
-
Model K
View ProductOur Model K unit is one of the most popular in the product line. It is ideal for lab use or pilot production research.
Our micro-abrasive blasting solutions have set the standard for over 65 years.
We didn’t just invent micro-blasting technology — we created a complete micro-abrasive system that is built to do the job, and built to last. That’s why Airbrasive has earned the trust of so many prestigious institutions around the world.

Machines Built to Last
Built to work long hours, day after day. Many Airbrasive machines have been working around-the-clock for over 25 years.

Highest Quality Powder
Airbrasive is the only manufacturer to triple sift its powders to guarantee particle size uniformity to the micron.

Exceptional Service
Within one day of your call, our team will have a solution in place that best suits your needs.
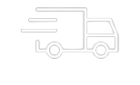
Fast Delivery
We ship your product within 24 hours from the time your order is placed.